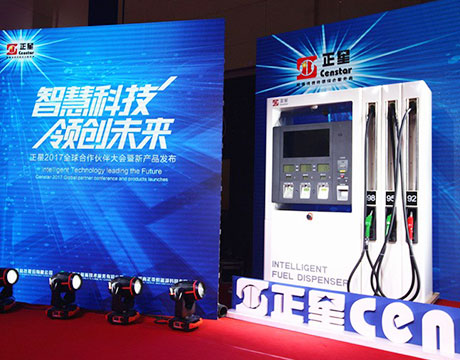
Hydrogen Production: Natural Gas Reforming Department of
Natural gas contains methane (CH 4) that can be used to produce hydrogen with thermal processes, such as steam methane reformation and partial oxidation. Although today most hydrogen is produced from natural gas, the Fuel Cell Technologies Office is exploring a variety of ways to produce hydrogen from renewable resources.

High Temperature Fuel Cell Tri Generation of Power, Heat
Operation on natural gas from Janu • Installation completed in June, 2011 (including ADG skid) • Operation on ADG: 3,522,591 SCF processed & used • Electricity produced: 605,512 kWh • Hydrogen produced: 6,400 lbs (2,902 kg) • Steady State performance demonstrated • Significant challenges with grid interconnection, power

Hydrogen Fuel Cost vs Gasoline Hydrogen Energy Systems LLC
Hydrogen is measured by the kilogram. 1 kilogram is 1 gallon of gasoline equivalent (gge). 2. $ /gallon + $ /kg (gge) Refining Costs = $ =
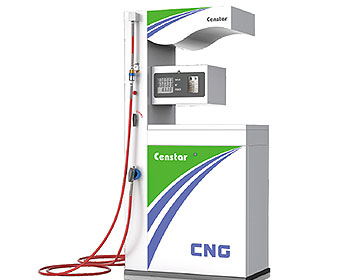
Cost and Performance Comparison of Stationary Hydrogen
hydrogen 5. Hydrogen gas purification The difference between SMR and ATR is how heat is provided to activate the endothermic steam reforming reaction. In SMR, the catalyst is contained in tubes that are heated by an external burner. In ATR, a portion of the natural gas is burned to raise the temperature of the process gas before it contacts the catalyst.
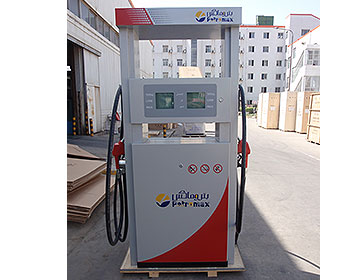
A comparative overview of hydrogen production processes
It is estimated that a typical route of biomass gasification steam reforming PSA, requires 2.4 TJ of primary energy input per TJ of hydrogen , and for a plant with an expected hydrogen output of 139,700 kg/day and cost of biomass in the range of 46 80 $/dry ton the hydrogen production cost is expected to be $/kg .
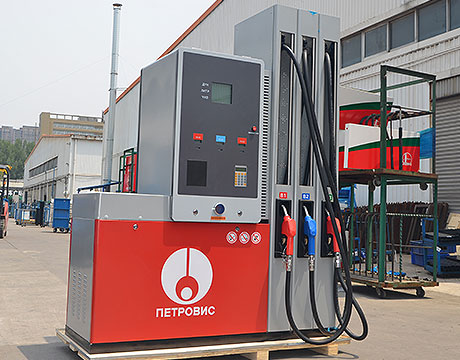
Hydrogen economy Wikipedia
General Atomics predicts that hydrogen produced in a High Temperature Gas Cooled Reactor (HTGR) would cost $ /kg. In 2003, steam reforming of natural gas yielded hydrogen at $ /kg. In 2005 natural gas prices, hydrogen costs $ /kg.
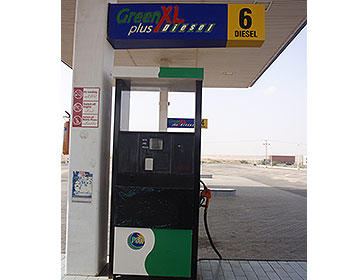
CURRENT STATUS AND FUTURE PROSPECTS OF
This paper descries current status and future prospects of hydrogen production technology at Tokyo Gas, focusing on a new concept membrane reformer technology for highly efficient and compact hydrogen production systems, construction and demonstration of hydrogen refueling station using LPG and natural gas feedstock for fuel cell electric
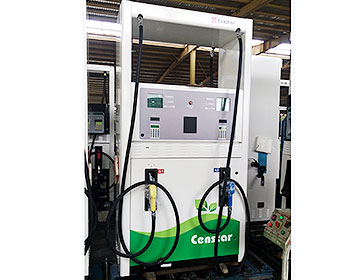
Distributed Hydrogen Production via Steam Methane Reforming
Distributed production of hydrogen from natural gas utilizes small scale steam methane reforming technology. The advantages of distributed hydrogen production are the production unit can be located at the consumer refueling site, the unit capacity can be tailored to the site’s fueling requirements, and this approach eliminates the need for an extensive hydrogen delivery infrastructure.

Hydrogen Technical Analysis on Matters Being Considered by
• Gaseous hydrogen generated at the refueling station from natural gas by steam methane reforming (SMR), stored as a compressed gas at 5000 psi and dispensed to the vehicle as a gas.

8. Hydrogen Production Technologies The Hydrogen Economy
The primary ways in which natural gas, mostly methane, is converted to hydrogen involve reaction with either steam (steam reforming), oxygen (partial oxidation), or both in sequence (autothermal reforming).
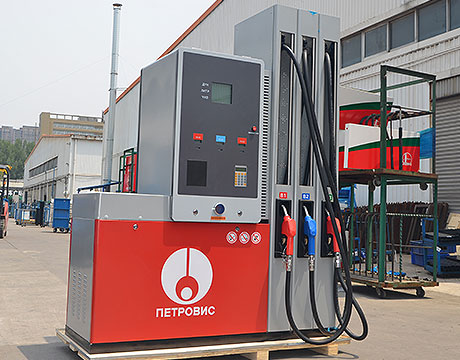
Hydrogen Production Challenges Stanford University
Hydrogen Production / Delivery Costs 02 4 6 8 10 Production Distribution Dispensing H 2 Cost ($ for energy equivalent of 1 gallon of gasoline, ex. tax) Central Natural Gas, SMR, Liquid Dist. Coal Gasification, Liquid Dist. Retail Natural Gas SMR Retail Gasoline Reformer Central Natural Gas SMR, Pipeline Dist. Central Water Electrolysis, Liquid
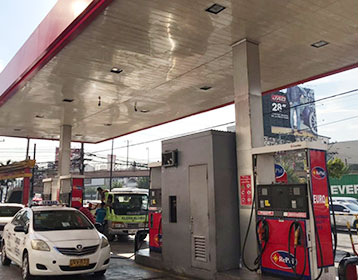
Hydrogen Production By Steam Reforming Chemical
Steam reforming of natural gas at petroleum refining facilities is the predominant means of producing hydrogen in the chemical process industries (CPI). Areas where hydrogen is heavily consumed include ammonia production, the cryogenics industry and methanol production (Table 1)[1].
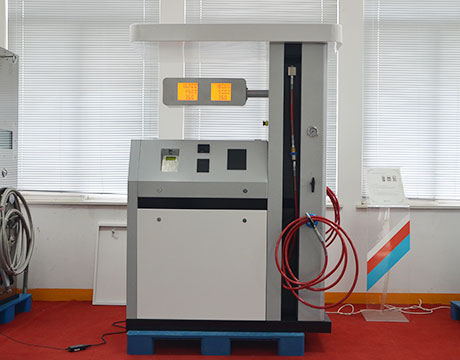
“Overview of the market segmentation for certifhy
“Overview of the market segmentation for HENG Hydrogen Enriched Natural Gas HRS Hydrogen Refueling Station ICE Internal Combustion Engine kg kilograms km kilometers by steam methane reforming (SMR) of natural gas, coal gasification and as a results of cracking of

Summary of Hydrogen Production and Storage Systems
SMR produces a hydrogen rich gas that is typically on the order of 70 75% hydrogen on a dry mass basis, along with smaller amounts of methane (2 6%), carbon monoxide (7 10%), and carbon dioxide (6 14%) (Hirschenhofer et al., 2000).
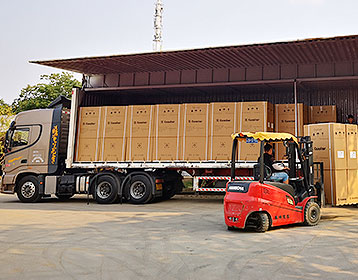
Hydrogen Station Compression, Storage, and Dispensing
from $ /kg to $ /kg of hydrogen for the forecourt production from natural gas with a base case of ~$ /kg of hydrogen. Again, uncertainties in compressor costs , efficiency, and installation factors caused a wide variance in projected cost s. These costs were evaluated using the H2A Current Forecourt Production from Natural Gas Model
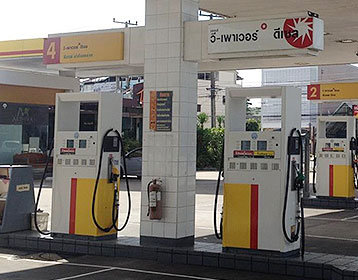
Hydrogen Station Cost Estimates NREL
timeframe when typical new stations resemble EC stations, with a capacity of 450 kg/day and a capital cost of $2.8 million per station. On a capacity basis, this capital cost is $6,220 per kg/day of station capacity. This is a 62% reduction in capital cost per capacity compared to SOTA stations.

About Hydrogen Fuel Cell Vehicles (They're Not Clean)
Time To Come Clean About Hydrogen Fuel Cell Vehicles. Twitter; natural gas steam reforming process. However, when FCVs are run on hydrogen reformed from natural gas
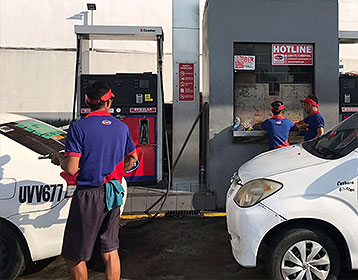
Alternative Fuels Data Center: Hydrogen Production and
Natural gas reforming using steam accounts for the majority of hydrogen produced in the United States annually. A synthesis gas can also be created by reacting coal or biomass with high temperature steam and oxygen in a pressurized gasifier, which is converted into gaseous components—a process called gasification. The resulting synthesis gas contains hydrogen and carbon monoxide, which is reacted
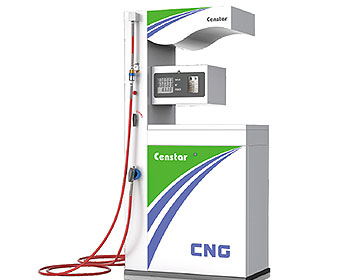
SENATE BILL 1505 ENVIRONMENTAL STANDARDS FOR
SMR Processes & Components Steam Methane Reformer Natural Gas compressor Cooling fans & Blowers Controller PSA motor H2 Compression Storage Dispensing Non Renewable Natural Gas Electrical 60 kg of 10,000 PSI Hydrogen output 33% Renewable mmBtu / 1,720 kwhr 600 kWhr Renewable Biogas mmBtu / 1,160 kwhr Non Electrical 9.8 mmBtu 2880 kWhr 600 kWhr

April: Producing industrial hydrogen from renewable energy
(Assumptions : CAPEX of electrolyzers USD 850/kW, WACC 7%, lifetime 30 years, efficiency 74%; cost of hydrogen from SMR USD 1 to 3/kg, cost of CCS USD /kg H 2 (~USD 75/tCO 2)) Places that meet these two conditions low prices and a high utilization factor could be found in sunny, windy regions with the right combination of solar plants and wind farms.

Distributed Systems for Hydrogen Production from City Gas
using a compressor to at least 7 MPa and 29°C before being cooled to room temperature, and then all CO2 in the off gas was removed by a vapor/liquid separation tank. In estimating CO2 emissions caused by electric power consumption, we assumed the CO2 emission intensity of kg/kWh (reported by Tokyo Electric Power for 2006).

Natural Steam Methane Reforming (SMR) Inside Mines
Raw material costs (primarily natural gas) Electricity Other operating expenses (staff, ) Recovery of capital invested • Minimum is to cover cost of natural gas & power • Example Natural gas $ per million BTU (as of Ma ) = $ per kmol CH 4

Used Hydrogen (HyCo) & Synthesis Gas (Syngas) Plants for
Learn More About Hydrogen (HyCo) & Synthesis Gas (Syngas) Plants Syngas, or synthesis gas, is a fuel gas mixture consisting primarily of hydrogen and carbon monoxide. Syngas is mainly used as fuel to generate electricity and as feedstock to produce various chemicals such as ammonia, methanol, methane, dimethyl ether, etc.
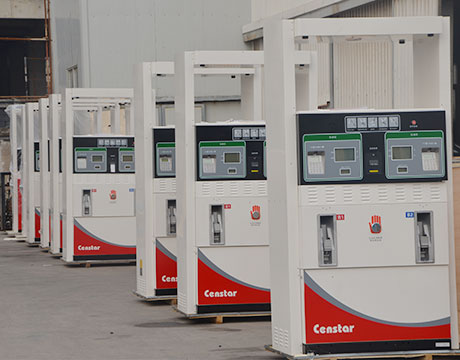
Steam Methane Reforming Hydrogen Production Air Liquide
Steam Methane Reforming Hydrogen Production. In the steam reforming process, a desulfurized hydrocarbon feedstock (natural gas, refinery offgas, liquefied petroleum gas or naphtha) is pre heated, mixed with steam and optionally pre reformed before passing a catalyst in a proprietary top fired steam reformer to produce hydrogen,

Gaseous Hydrogen Compression Department of Energy
Gaseous Hydrogen Compression. Centrifugal compressors rotate a turbine at very high speeds to compress the gas. Hydrogen centrifugal compressors must operate at tip speeds 3 times faster than that of natural gas compressors to achieve the same compression ratio because of

Micro Hydrogen Generator by SMR_Ally Hi Tech Co., Ltd.
Ally Hi Tech is one pioneer who is engaged in the solution of the micro hydrogen generator based on the natural gas steam reforming (SMR) technology. Ally delivered a hydrogen generator with a capacity of 50 Nm 3 /h based on SMR for the hydrogen station which is used to refuel the Fuel Cell Vehichle for Beijing Olympics in 2008.

April: Producing industrial hydrogen from renewable energy
(Assumptions : CAPEX of electrolyzers USD 850/kW, WACC 7%, lifetime 30 years, efficiency 74%; cost of hydrogen from SMR USD 1 to 3/kg, cost of CCS USD /kg H 2 (~USD 75/tCO 2)) Places that meet these two conditions low prices and a high utilization factor could be found in sunny, windy regions with the right combination of solar
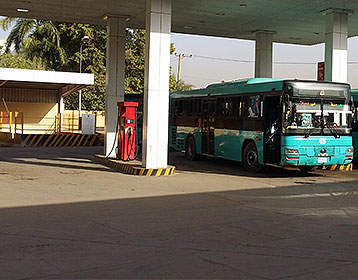
Danish team electrifies steam methane reforming for
Using very high temperatures and steam, SMR reformers convert methane into carbon dioxide and hydrogen. However, this widely used method also has a significant CO 2 footprint; not only is the greenhouse gas produced as a byproduct of the reaction, fossil fuel burning furnaces are used to supply the heat required to drive the reactions.
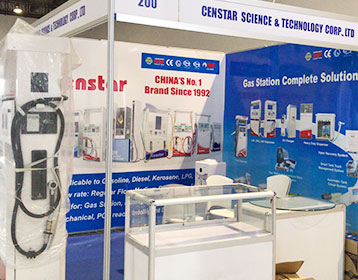
New Bus ReFuelling for European Hydrogen Bus Depots
In contrast, a steam reformer uses hydrocarbons, predominantly methane, and water vapour and produces hydrogen within a catalytic reaction (steam methane reformer SMR). Two different technologies are commonly used for the electrolysis of water: alkaline electrolysers and proton membrane exchange (PEM) electrolysers.
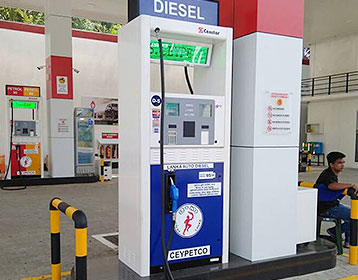
DOE Hydrogen and Fuel Cell Technical Advisory Committee
generate hydrogen. US natural gas reserves are: Natural gas 238 TCF Unconventional gas streams 400 TCF Shale formations expected 1,200 TCF •If all U.S. transportation 300MM vehicles where to convert to hydrogen it would require ~10 TCF natural gas. Current NG consumption is 25 TCF.
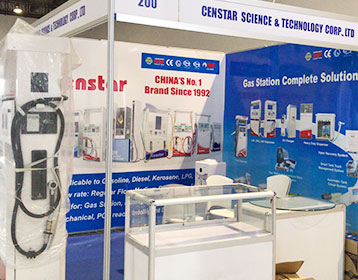
Prospects for Hydrogen in the Future Energy System
apparent. Large scale thermochemical conversion of fossil fuels (natural gas or coal) is currently the least costly way to make hydrogen in terms of both the specific capital cost ($/kW) and the levelized cost of hydrogen ($/kg). With carbon capture, greenhouse gas emissions can be significantly reduced, at relatively modest cost.

Hydrogen Fueling Station Cooper Union
The hydrogen storage system is designed to store a day’s worth of hydrogen. It consists of a series of four compression stages to compress the hydrogen to 820 atm. The hydrogen is kept in 24 carbon fiber tanks that hold the hydrogen for the fueling station.

Hydrogen InfrastructureHydrogen Infrastructure
Hydrogen InfrastructureHydrogen Infrastructure Nick Mittica Air Products and ChemicalsAir Products and Chemicals SMR POX STEAM / POWER CUSTOMER(S) Offgas Fuel) REFORMING PSA GASEOUS PIPELINE MEMBRANE 100 kg/day Syngas Shift Hydrogen Natural Gas Feed Compressor

Natural Gas to Hydrogen (H) processdesign
With the increased production of natural gas and the corresponding drop in price, steam reforming is a profitable method to produce hydrogen. The goal of this project is to design, optimize, and economically analyze a steam reforming process that will produce % hydrogen from a feedstock of natural gas.

The Status of Renewable Hydrogen and Energy Station
Hydrogen is Hydrogen is NotNot Always Good forAlways Good for Env’t 120 100 80 60 40 20 0 20 40 60 80 100 NG central G H2NG central w/steam G H2NG central L H2NG central w/steam L H2NG station G H2NG station L H2Electrol. US mix G H2Electrol. US mix L H2Electrol. CCNG G H2Electrol. CCNG L H2Electrol. Nuclear G H2Electrol.

Renewable Fuels: Manufacturing Ammonia from Hydropower
An average scale ammonia plant produces 500 to 1,000 metric tons of ammonia per day. That results in the use of a tremendous amount of natural gas. For example, the amount of natural gas needed for one day's production of ammonia at that average scale plant would heat 850 to 1,700 homes during a typical northeastern U.S. winter for one month.

Hydrogen Fueling Stations Infrastructure
series of reactors, a purification system PSA, buffers and hydrogen compressor, filters, air dryers and compressors, and hydrogen dispensing pumps (Figure A1).[3] The approximate hydrogen fueling capacity of this type station is 100 1000 kg/day depending on the size of the reformer and the number of dispensing pumps.[4] 2.2.

Understanding Natural Gas Compressor Stations
Compressor stations are an integral part of the natural gas pipeline network that moves natural gas from individual producing well sites to end users. As natural gas moves through a pipeline, distance, friction, and elevation differences slow the movement of the gas, and reduce pressure. Compressor

Mallnow Natural Gas Compressor Station
Mallnow Natural Gas Compressor Station 5 The steam turbine compressor unit was installed whilst the Mallnow station was in operation. MAN Diesel & Turbo’s knowledge in the integration of different types of turbomachinery made a significant contribution to the optimization of the Mallnow station. during their frequent use in the transportation
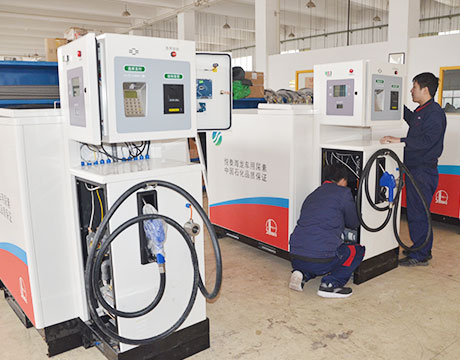
Steam reforming Linde Engineering
Steam reforming Steam reforming is the most widespread process for the generation of hydrogen rich synthesis gas from light carbohydrates. The feed materials natural gas, liquid gas or naphtha are endothermically converted with water steam into synthesis gas in catalytic tube reactors. Process heat as well as flue gas are used for

Distributed Hydrogen Production FuelCell Energy
emissions per kg of hydrogen produced are about 40% less than conventional SMR production when using natural gas fuel. When using biogas fuel the hydrogen is carbonfree. The price of the hydrogen is reduced by the revenue coming from production of power the co and heat from these fuel cell systems.

Hydrogen Production: Natural Gas Reforming Department of
Most hydrogen produced today in the United States is made via steam methane reforming, a mature production process in which high temperature steam (700°C 1,000°C) is used to produce hydrogen from a methane source, such as natural gas. In steam methane reforming, methane reacts with steam under 3 25 bar pressure (1 bar = 14.5 psi) in the presence of a catalyst to produce hydrogen, carbon
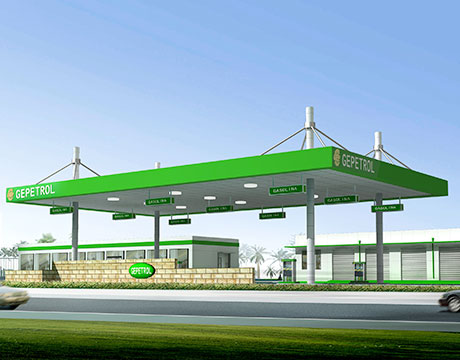
Appendix G: Hydrogen Production Technologies: Additional
Using currently available technology, the CO 2 emissions are about 19 kg CO 2 per kilogram of hydrogen produced, compared with approximately 10 kg CO 2 per kilogram of

Being A Gas Pumping Station Operator: What You Really Do
Gas Pumping Station Operators operate steam, gas, electric motor, or internal combustion engine driven compressors. Transmit, compress, or recover gases, such as butane, nitrogen, hydrogen, and natural gas. We asked Gas Pumping Station Operators

On Site Steam Methane Reforming Unit for Hydrogen
Although the process chemistry remains the same for a small scale SMR (50 100 kg/day H 2) when compared to a large scale refinery SMR, there are severe economy of scale penalties related to capital costs for small scale SMR based hydrogen energy stations. In addition, natural gas reforming is a relatively high temperature process.